Ariane 6: Analysis of Design Characteristics & Enabling Technologies
- Setondji V. Nahum
- May 16, 2021
- 20 min read
Course: Space Mission & Launch Operations
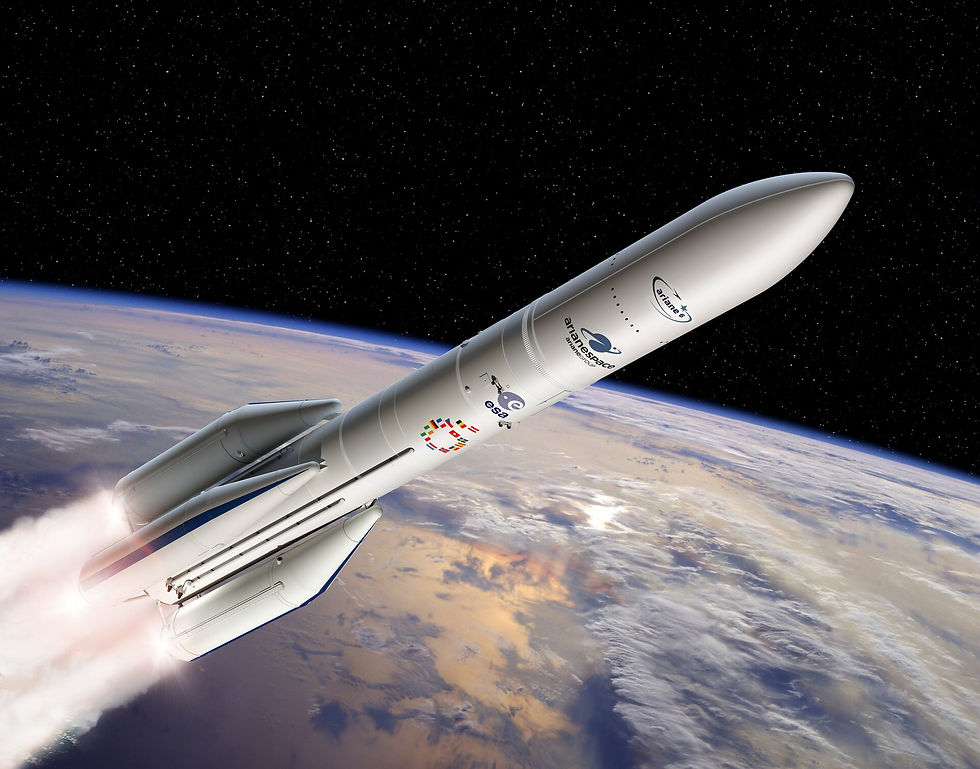
Introduction
The earliest theory of gravity is asserted by Nicolas Copernicus through his heliocentric theory that describes the earth as a planetary body orbiting the sun. In fact, an earth-centered system exhibits flawed characteristics and spiraling motions from other solar planets due to the gravitational pull of the sun or their orbiting motion around the sun. Based on the written history of Science and Astronomy, renowned scientists such as Kepler, Galileo, Newton, and Einstein researched, developed, and improved Copernicus heliocentric theory. They essentially unlocked the concept of gravity.
Gravity is a pulling force that is exerted by all matters. It is commonly defined as the universal force of attraction acting between all matters. The National Aeronautics and Space Agency (NASA) define gravity as the force by which a planet or other body pull objects toward its center (NASA, 2020). Thus, departing earth and exploring the space environment requires the capability to escape earth’s gravitational pull. The total energy of an Earth-escape parabola is zero. It is used to derive the second cosmic velocity or escape velocity which has been determined to be approximately 11.2 km/s. This has required the use of a space launcher system which must carry a satellite to altitudes higher than 200 km to remain in orbit due to the high air drag at lower altitudes. To overcome Earth’s gravitational pull and drag forces, a launcher system must be capable of achieving a velocity of approximately 10 km/s to launch a satellite into Low Earth Orbit (Uhlig et al., 2015).
Launch vehicles payload and performance capabilities must meet defined mission payload and requirements. Their design requires the development of solutions to significant engineering problems which include mitigating the effects of acoustics and vibrations levels, the impact of sudden static acceleration and mechanical shock from ignition and separation of the vehicle stages, and the effects of fairing jettison and spacecraft separation (Uhlig et al., 2015). Given the new trends in the space launch service market, a launcher program must balance the necessity of system improvements and innovations, the obligation to meet vehicle design and safety requirements, and the need to keep vehicle research, development and operational cost at a minimum. One of the most intriguing launch vehicles being currently designed is Ariane 6. It is the new generation launcher from the Ariane launch vehicle family. The Ariane 6 launch system is reportedly built to achieve optimum vehicle performance at a lower production and operations cost (Ariane, 2021). Thus, what are the design characteristics and enabling technologies of the Arianne 6 launch system for flightworthiness, reliability, and survivability?
A newly designed launch pad, grid-stiffened composite materials, a roll control system, re-ignitable engines, a very low fairing separation shock system, an upper liquid propulsion module modularity, an attitude control system, a multi-adapters configuration and thermal insulations optimize the Ariane 6 airframe structural integrity, system safety and operational capabilities (Ariane, 2021).
Bibliography
The table below provide details of essential resources used for the research.
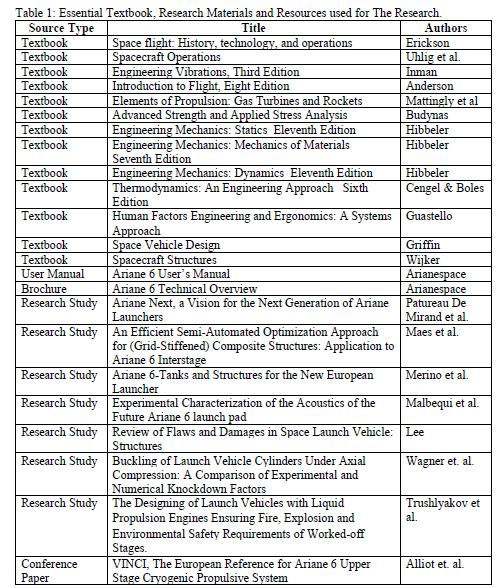
Problem Statement, Research Question and Research hypothesis
Space launch vehicles shall be designed to safely propel and release spacecraft and or satellites into a pre-defined orbit. Their payload and performance capabilities must meet defined mission payload and requirements.
Problem Statement
Launch vehicles design requires the development of solutions to significant engineering problems which include mitigating the effects of acoustics and vibrations levels, the impact of sudden static acceleration and mechanical shock from ignition and separation of the vehicle stages, and the effects of fairing jettison and spacecraft separation (Uhlig et al., 2015). Given the new trends in the space launch service market, a launcher program must also balance the necessity of system improvements, the obligation to meet vehicle design and safety requirements with the demand to keep vehicle research, development, and operational cost at a minimum. The Ariane 6 launch system is required to achieve system improvements and optimum vehicle performance at a lower production and operations cost (Ariane, 2021).
Research Question
What are the design characteristics and enabling technologies of the Arianne 6 launch system for flightworthiness, reliability, and survivability?
Research Hypothesis
A newly designed launch pad, grid-stiffened composite materials, a roll control system, re-ignitable engines, a low fairing separation shock system, an Upper Liquid Propulsion Module (ULPM) modularity, an attitude control system, a multi-adapters configuration and thermal insulations optimize the Ariane 6 airframe structural integrity, system safety and operational capabilities (Ariane, 2021).
Literature Review
Ariane 6 is the new generation launcher from the Ariane launch vehicle family. It is reportedly built to achieve optimum vehicle performance at a lower production and operations cost. In the article titled: Ariane Next, a Vision for the Next Generation of Ariane Launchers, Patureau De Mirand, Bahu and Gogdet mainly discuss ArianeGroup’s vision for the next Ariane launcher to be developed after Ariane 6. But the article’s references to Ariane 6 indicate the use of composite materials to manufacture its liquid propellant tanks and the Upper Liquid Propulsion Module (ULPM) which is essentially composed of metallic tanks and structural elements. The program reportedly saved approximately 1000 kg with its new metallic tanks structure and its primary and secondary stage structure. It shall also achieve additional mass savings of approximately 1000 kg with the redesign of its Upper module. The Ariane 6 exhibits improved capabilities and increased flexibility that support a significant minimization of development and operational costs ( Patureau De Mirand, Bahu & Gogdet, 2020).
The Ariane 6 launch system’s composite structure is discussed in the article titled: An Efficient Semi-Automated Optimization Approach for (Grid-Stiffened) Composite Structures: Application to Ariane 6 Interstage. Maes, Pavlov and Simonian present characteristics of grid stiffened composites structures and their application to Ariane 6 interstage. Grid stiffened composites offers significant improvements in structural efficiency but have presented multiple computational and analytical challenges for engineers. Through the use of a structural analysis method characterized by the use of a generic genetic algorithm, the authors demonstrated a potential weight savings of 20 % for the Ariane 6 interstage structure ( Maes, Pavlov & Simonian, 2019).
Design configurations of the Ariane 6, its upper liquid propulsion module (ULPM), its lower liquid propulsion module (LLPM), and other components are discussed in the article titled: “Ariane 6- Tanks and Structure for the New European Launcher”. First, Merino et al. present two configurations for the launch vehicle. The Ariane 62 is designed for government projects while the Ariane 64 is designed for commercial projects which often include the simultaneous launch of multiple satellites. The authors report that the modules, tanks, and other hardware components are compliant with ISO 16290 which is the European standard for space systems hardware technology readiness (Merino et al., 2017)
Structural flaws and damages in space launch vehicles are discussed in the article: “Review of Flaws and Damages in Space Launch Vehicle: Structures.” Lee & Dhital report that although they contribute to high structural efficiency, advanced grid-stiffened fairing structures are prone to multiple failure issues that are often caused by rib crippling, skin pocket buckling and global Euler buckling. This often results in joint failure due to shear, joint failure due to skin pull-off and joint failure due to skin peeling or bending. Buckling occurs due to the low stiffness of the skin (Lee & Dhital, 2013).
The Ariane 6 propulsion system is discussed in the conference article titled: “VINCI, the European Reference for Ariane 6 Upper Stage Cryogenic Propulsive System.” Alliot, Delange & Lekeux present the VINCI engine as the cryogenic upper stage engine of the Ariane 6. It is a 180 kN re-ignitable engine designed for high reliability, high performance, and low recurring costs. It is equipped with a hydrogen turbo-pump and an optimized combustion chamber cooling circuit. Its slow actuator rate by-pass valves were selected for the purpose of minimizing operational cost (Alliot, Delange & Lekeux, 2015).
The Ariane 6 is discussed in the textbook titled: “Handbook of Small Satellites.” Pelton and Madry report that the vehicle is designed to support significantly lower operational costs than the previous Ariane models. It is designed with a modular configuration and liquid propellant modules are part of its core stages. The A62 is equipped with two rocket boosters and has the capability of launching 5 metric tons to geosynchronous orbits. The A64 is equipped with 4 rocket motors and has the capability of launching 11 metric tons into geosynchronous orbits (Pelton & Madry, 2020).
The recovery of the engine and engine frame of the Ariane 6 is discussed in the research article titled: “A Recovery System for the Key Components of the First Stage of a Heavy Launch Vehicle.” Dek et al. present a feasibility study for recovering the Ariane 6 Vulcain engine aft bay. The authors proposed a method constituting of the use of an inflatable aeroshell for protection and deceleration during re-entry, the use of parafoil to enable a controlled gliding flight and the use of a helicopter to complete the retrieval. This recovery system can reportedly be integrated with the Ariane 6 design with no impact to its theory and method of operations. But most importantly, the recovery system can foster a 15% savings for each Ariane 6 launch operation (Dek et al., 2020).
Solid rocket motor improvement opportunities and enabling technologies for the Ariane 6 design based on lessons learned from the Ariane 5 launch vehicle are presented in the research article titled: “Solid Rocket Motors Technologies for Ariane 6”. Boury et al. completed a comparative study of multiple launcher configurations focused on rocket motors. Significant performance improvements are exhibited by the P 180 and the P110 rocket motors. They essentially accommodate higher spacecraft payload capacity. The authors discuss how the use of three or more P-135 rocket motors for both the first and second stages correlate to high production rate, and low operational and maintenance costs for the motor. The authors also present two engineering problems specific to motor design: producing cost-effective large motor cases and designing a system that generate low pressure and thrust oscillation (Boury et al., 2013).
Design configurations and safety requirements of the Ariane 6 launcher are discussed in the article titled: “ Derivation of the French Space Operation Act Requirements in the Specifications of the Future European Launcher Ariane 6.” Dias report that the Ariane 6 is configured with a Vinci engine that powers its upper liquid propulsion module (ULPM) and a Vulcain engine that powers its lower liquid propulsion module (LLPM). The vehicle’s upper part includes a fairing, the launch vehicle adaptor, and a payload adaptor fitting. The Ariane 6 launcher is compliant with the French Space Operation Act (Dias, 2018).
A preliminary study of acoustic noise generated by the Ariane 6 engines at lift-off is presented in the research study titled: “Experimental Characterization of the Acoustics of the Future Ariane 6 Launch Pad”. Malbéqui, Davy, and Bresson demonstrate that acoustic noises at lift-off and low altitude are mitigated by the use of covered trenches. Upon describing the Ariane 6 launch pad as a set of two covered trenches which control the flow of boosters and engines jet plumes, the authors present how the highest sound pressure are generated at altitude approximately equivalent to twenty times the launcher’s engine nozzle diameter. They determine that noise radiation at low heights is generated by the trenches. The authors also established that sound pressure at heights approximately equivalent to twenty times the launcher engine nozzle diameter is primarily generated by the noise echoed on the trench roofs through a noise attenuating component and the pressure generated by jet plumes flowing onto the launch pad (Malbéqui, Davy, & Bresson 2015).
System requirements and operational concepts of the Ariane 6 space launch vehicle are discussed in the research study titled: “Ariane 6 Launch System Operational Main Drivers”. Resta et al. first present key system components and high level requirements. The Ariane 6 system components include a fairing with a height of 20 m, a dual launch system, an Upper Stage Liquid Propulsion Module, a re-ignitable Vinci-engine, a Lower Stage Propulsion Module, a Vulcain engine and solid rocket boosters. High level system requirements include the capability to operate from the Guiana Space Center, the capability of completing 12 launches per year, and a significant minimization of operational costs. The Ariane 6 operational concept goals include an improvement of system launch facilities and launch range operations, simple interfaces with the spacecraft, minimization of operations time and cost, quick post flight analyses and improved launcher processing cycles (Resta et al., 2019).
Methods and enabling technologies used to mitigate the effects of high temperature on the Ariane 6 Cryogenic Upper Stage sub-systems and components are discussed in the research article titled: “Thermal Control of The Cryogenic Upper Stage of Ariane 6” and completed by Burow et al. Components positioning measures are taken to ensure that electronic instruments that operate within the limits of room temperature are installed as far as possible from cryogenic tanks. Heat dissipating units are installed near heat absorbing components to assist with maintaining both instrument types within required temperature limits. Thermal fillers are used to improve coupling while thermal washers are used to minimize it. Helium conditioning is used to dilute leaks and prevent humidity. Thermal protection measures taken include the use of closed cell foams to prevent contact between cold structures and nitrogen. Ablative materials are used to minimize structural thermal loads. Multi-layers insulations are used to minimize the effects of heat fluxes emitted by the attitude control system on adjacent materials. Electrical heaters are used to regulate systems and component temperatures in cold environments. Surface finishes such as high-temperature resistant coatings and optical coatings are used to protect against the truly detrimental effects of extreme heats, and solar and infrared fluxes (Burow, 2019).
A thorough description of program objectives, design configurations and performance capabilities of the Ariane 6 launch system is provided by ArianeGroup in the document titled: “Ariane 6 User Manual.” The Ariane 6 mission ranges include geosynchronous orbits, polar and sun-synchronous orbits, and medium-earth orbits. The vehicle components include 14 meters or 20 meters high payload fairing, a payload adapter, a dual launch structure, a launch vehicle adapter, an upper liquid propulsion module (ULPM), a Vinci engine re-ignitable in orbit, a lower liquid propulsion module (LLPM), P120 solid rocket motors and a Vulcain engine. The A 64 is capable of launching a payload of up to 11500 kg into standard geosynchronous transfer orbits. The A 62 is capable of launching a payload of up to 6000 kg into sub-geostationary transfer orbits. For geosynchronous transfer orbits mission altitudes and a direct ascent profile, the mission duration is an hour from lift-off to spacecraft separation into its final orbits. The effects of static acceleration, acoustic noise and vibrations are mitigated through defined stiffness requirements and limit levels for quasi-static loads. The range of sinusoidal excitations at the spacecraft base are predetermined and composite materials are among the solutions used to diffuse noise and vibrations. Clamp-based tests are used to determine the vehicle ability to withstand shocks during fairing jettison, upper stage separation and the spacecraft separation. Two composite shells with thermal protection and anti-static paint are used to maintain the payload fairing structural integrity (ArianeGroup, 2020). The fairing is mainly composed of an internal acoustic protection, two umbilical pneumatic plugs, vent ports, a door for conditioning during transportation, a very low separation shock system, a standard harness, two doors with a diameter of 300 mm and a 12 spring package. The launch vehicle adapter is configured for transitions between the upper liquid propulsion module (ULPM) and the payload adapter. It is essentially composed of a conditioning deflector, two umbilical electrical plugs, two raceway connectors plates, two core brackets, two brackets for fairing jettison connectors and a tight membrane that isolates the fairing from the upper liquid propulsion module (ArianeGroup, 2020).
The main objectives and the defined ideal payload conditions for the Ariane 6 launch vehicles are discussed in the research article titled: “ Design of Launcher Towards Spacecraft Comfort: Ariane 6 Objectives”. Mourey, Lambare and Valbuena indicate that the principal goals of the Ariane 6 program include providing Europe with an access to space without using funds from the public sectors and providing European customers with space launch services independent from other world regions. The Ariane 5 configuration is significantly used as a base model to define payload environment and payload comfort criteria. Noise, vibrations, and shock levels of the new launch vehicle are to be lower or equal to levels achieved for the Ariane 5. Based on lessons learned from previous models, values for the low frequency dynamic environments are set to 0- 100 hz. The standard payload adaptor fitting interface diameter is set at 1780 mm. Payload stability and comfort are to be improved by considering criteria such as maximum accelerations, aeroshape, lift-off environment and boosters pressure oscillations. A harmonic load case is to be used to minimize vibrations and specifically the boosters’ thrust oscillations. Solid propellant boosters of the Ariane 6 will not be segmented. A monolithic loading configuration is to be used because they generate significantly less vibration levels. Engines design improvement objectives included limiting excitation levels. Vibration and dynamic levels of the upper stage and the spacecraft are to be minimized through the use of a payload isolation device and a dynamic isolator. Shocks due to fairing separation are to be limited by ensuring that the shock levels generated by the space launch vehicle is less than shocks levels produced by the satellite or payload separation system ( Mourey, Lambare & Valbuena, 2014).
Computer architectures, communication buses and other innovative digital engineering technologies pertaining to the Ariane 6 space launch vehicle are discussed in the study titled: “Ariane Launchers Digital Engineering: Stakes and Challenges”. Polonowski and Clavier highlight how critical such digital system components are to the launch vehicle reliability, performance, and cost. Communication bandwidth for the Ariane 6 vehicle has been improved by a factor of 100 to 1000 compared to the previous model. This accommodates the use of Time Triggered Ethernet (TTE) for the Ariane 6 vehicle. TTE is selected for the Ariane 6 because of the simplicity of system level development of communication logics. The use of fiberoptics significantly improve communication speeds and accommodate significant mass savings for the upper stage module. Despite the selection of TTE for the Ariane 6, the use of a Time Sensitive Network (TSN) shall be thoroughly evaluated because it significantly improves real-time communication capabilities of the system and minimizes latency. A TSN is ideal for real time and high reliability applications. TTE and TSN are ideal for safety critical and real time applications because they minimize system latency and improve system redundancy (Polonowski & Clavier , 2019).
The concepts of thrust and acceleration are essential to the motion of the Ariane 6 and discussed in the textbook titled: “ Engineering Mechanics: Dynamics”. Hibbeler shows that engine thrust is a reaction force that propels the launcher upward by opposing the system weight and drag forces, while acting in an opposite direction to the exhaust velocity (Hibbeler, 2007).
Analysis
An analysis of the Ariane 6 launch vehicle must encompass the main system components, the launcher performance capabilities, a comparative study against the Soyuz and the Space Launch System (SLS) and a comparison of the Ariane 6 expandable space launch vehicle concept to SpaceX re-usable space launch vehicle concept.
Brief System Description

Figure 1: Ariane 6 Launch System Description. ArianeGroup. (2021, February). Ariane 6 User Manual. https://www.arianespace.com/wp-content/uploads/2021/03/Mua-6_Issue-2_Revision-0_March-2021.pdf
The Ariane 6 primary system components include a payload fairing, a payload adapter, a dual launch structure, a launch vehicle adapter, an Upper Liquid Propulsion Module (ULPM), a Vinci re-ignitable engine, a Lower Liquid Propulsion Module (LLPM), P 120 solid rocket motors and a Vulcain engine. The vehicle’s mission ranges include geosynchronous orbits, polar and sun-synchronous orbits, and medium-earth orbits. The A 64 model is equipped with 4 rocket boosters and is capable of launching a payload of up to 11500 kg into standard geosynchronous transfer orbits. The A 62 model is equipped with 2 rocket boosters and is capable of launching a payload of up to 6000 kg into sub-geostationary transfer orbits. For geosynchronous transfer orbits mission altitudes and a direct ascent profile, the mission duration is an hour from lift-off to spacecraft separation into its final orbits (ArianeGroup, 2020).
Flightworthiness, reliability, and survivability are ensured through the development of current and pioneering solutions to launcher design challenges and the integration of innovative enabling technologies. The effects of acoustic noises, sudden static acceleration and vibrations on the spacecraft and its structure at lift-off are mitigated through the use of covered trenches (ArianeGroup, 2020). Defined stiffness requirements and limit levels for quasi-static loads and composite materials which include grid-stiffened composites are also used to absorb and diffuse noise and vibration levels across the spacecraft structure. Mechanical shock from ignition, separation of the vehicle stages and fairing jettison are primarily mitigated through the use of clamps and composite materials. Maximum shock levels that could be withstood by the system are pre-determined during the system design phase through the use of clamp-based tests. Two composite shells with thermal protection and anti-static paint are used to maintain the payload fairing structural integrity (ArianeGroup, 2020). Vibration and dynamic levels of the upper stage and the spacecraft are to be minimized through the use of a payload isolation device and a dynamic isolator. Shocks due to fairing separation are limited by ensuring that shock levels generated by the space launch vehicle is less than shocks levels produced by the satellite or payload separation system ( Mourey, Lambare & Valbuena, 2014). Thermal protection measures taken include the use of closed cell foams to prevent contact between cold structures and nitrogen. Ablative materials are used to minimize structural thermal loads. Multi-layers insulations are used to minimize the effects of heat fluxes emitted by the attitude control system on adjacent materials. Surface finishes such as high-temperature resistant coatings and optical coatings are used to protect against extreme heats, solar and infrared fluxes (Burow, 2019).
Comparative Study Against the Soyuz and The Space Launch System
The Ariane 6 space launch vehicle concept follows the principle of expendable systems used for previous Ariane launch vehicle models, the renowned Russian Soyuz launcher and the newly designed Space Launch System (SLS) of the National Aeronautics and Space Agency (NASA). The market readiness, suitability and competitiveness, system efficiency, launch performance characteristics, payload capabilities, operational cost of the Ariane 6 shall be evaluated through a system level comparison with the Soyuz and the SLS. The re-ignitable in-orbit capability of the VINCI cryogenic upper stage engine of the Ariane is designed for high reliability, high performance, and low recurring costs (Alliot, Delange & Lekeux, 2015).
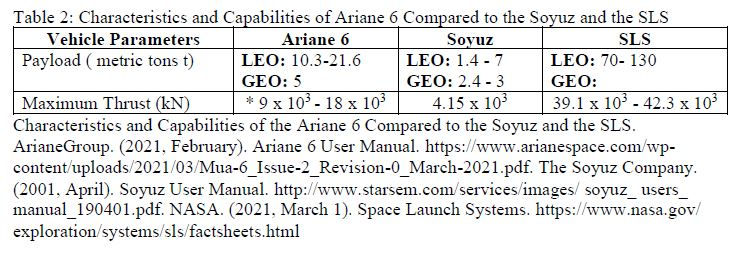
Table 2 indicates that the Ariane 6 displays much improved performance capabilities than the renowned Soyuz Launcher. This correlates to strong probability for program success in the European markets. Nevertheless, the Ariane 6 capabilities are significantly lower than NASA’s SLS which means that there are significant opportunities for improving the vehicle design. Contrary to the SLS, the Ariane 6 does not currently appear to have the capability of launching a payload directly into lunar orbit and beyond. Moreover, SpaceX re-usable launcher system concept currently offers the lowest operational cost per launch to customers. With low operational cost being a primary objective of the Ariane 6 launcher program, SpaceX re-usable launcher system present significant hurdles to the success of the Ariane 6 launcher.
Ariane Expandable System Concept Vs. SpaceX Re-Usable System Concept
The Ariane 6 expandable launcher concept is characterized by a non-recoverable single use system. Components such as the rocket motors ejects from the system and the fairings jettison during the vehicle ascension. Upper modules, lower modules, the payload, or spacecraft disconnect from the launcher through vehicle separation stages. The payload or spacecraft is launched into the pre-defined orbit and the upper stage is de-orbited and or transferred into a graveyard orbit (ArianeGroup, 2020). Contrary to expendable systems, re-usable space launch systems are essentially characterized by system recoverability. The capability for recovery of part or all of the systems components for later re-use are essential to the system design configuration and operational concept. Research and development costs of re-usable systems can be expected to be significantly higher because of the increased engineering and design complexity levels introduced by more stringent flightworthiness characteristics, higher system reliability, survivability and structural integrity parameters and requirements. Although higher research and development costs often correlate to higher operational costs per launch, SpaceX has demonstrated the capability of lower operational cost with its re-usable Falcon-9 launch vehicle. Space X currently retrieves and re-uses the vehicle core stages and plan on making the Falcon-9 fully re-usable.
Unofficial sources report that the operational cost per launch with the Ariane A62 is approximately 82 million dollars and 134 million dollars with the Ariane A64. Meanwhile, the operational cost per launch with the Falcon 9 is 62 million dollars. The Falcon 9 also launches approximately 8 metric ton of payload more than the A62. On average the Falcon 9 launch operation cost per metric ton is 7.5 million while the A62 operational cost per metric ton is 16.4 million dollars (Rich, 2018). This is important because it is supported by official sources which report an average operational cost per launch of 61.2 million with the Falcon 9 and an average operational cost per launch of 90 to 100 million dollars with the Ariane 6 (Reddy, 2018). This means that Ariane 6 must find new solutions to meet its objective of significantly low operational costs. Ariane 6 shall also expect to face strong competition from SpaceX in the European markets. A flightworthy, safe, and reliable re-usable space launcher system which offers the lowest launch operation cost in the market exhibits the most efficient system level characteristics and capabilities among launchers.
Conclusion
The Ariane 6 primary system components include a payload fairing, a payload adapter, a dual launch structure, a launch vehicle adapter, an Upper Liquid Propulsion Module (ULPM), a Vinci re-ignitable engine, a Lower Liquid Propulsion Module (LLPM), P 120 solid rockets motors and a Vulcain engine (ArianeGroup, 2020). The A64 model is equipped with 4 rocket boosters and is capable of launching a payload of up to 11500 kg into standard geosynchronous transfer orbits. The A62 model is equipped with 2 rocket boosters and is capable of launching a payload of up to 6000 kg into sub-geostationary transfer orbits. The effects of acoustic noises, sudden static acceleration and vibrations on the spacecraft and its structure at lift-off are mitigated through the use of covered trenches (ArianeGroup, 2020). Mechanical shock from ignition, separation of the vehicle stages and fairing jettison are mitigated through the use of clamps and composites. Maximum shock levels that could be withstood by the system are pre-determined during the system design phase through the use of clamp-based tests. Ablative materials are used to minimize structural thermal loads. High-temperature resistant and optical coatings protect against extreme heats, solar and infrared fluxes (Burow, 2019).
The Ariane 6 exhibits higher performance capabilities than the Soyuz. This indicates a strong probability for success in the European markets. But the Ariane 6 capabilities are lower than NASA’s SLS which means that there are opportunities for improving the vehicle design. Moreover, SpaceX re-usable launcher concept currently offers the lowest operational cost per launch. Given the objective of achieving lower operations costs and the competition presented by SpaceX Falcon 9, the Ariane 6 program must find system improvement opportunities that lower its launch services costs. This can be achieved through design configuration changes, integration of innovative enabling technologies, and minor changes to the system’s operational concept.
Recommendations
The Ariane 6 Space launcher is a remarkable system that exhibits very high system reliability, survivability, and structural integrity. Given the program objective of achieving significantly lower operations costs and the stiff competition presented by SpaceX, the Ariane 6 program must find system and operational concept improvement opportunities that lower its launch services cost. This can be achieved through design configuration changes, integration of innovative enabling technologies, and minor changes to the system operational concept. This is supported by Dek et al. who present a feasibility study for recovering the Ariane 6 Vulcain engine aft bay with no impact to its theory and method of operation. This is achieved through the use of an inflatable aeroshell for protection and deceleration during re-entry, the use of parafoil to enable a controlled gliding flight and the use of a helicopter to complete the retrieval. This solution fosters a 15% savings for every Ariane 6 launch operations (Dek et al., 2020).
The Ariane 6 capabilities are also limited by its design configuration. As shown by the comparative study displayed in Table 2, the Ariane 6 mission capabilities are significantly lower than NASA’s SLS. A potential solution is to integrate the Ariane 6 with a nuclear propulsion final stage that is ignited in orbit from a position that present no environmental pollution or radiation risks to planet Earth. Although nuclear fusion engines exhibit improved performance capabilities, they present significant challenges to this application due to vehicle size and mass requirements. Nevertheless, a final nuclear fission vehicle stage can be implemented through the configuration of a nuclear electric or nuclear thermal electric engine. This has the potential of providing the launcher with the capability of carrying spacecraft, satellites or any payload to orbits well beyond geosynchronous limits, lunar vicinities and the furthest orbits and distances ever achieved by mankind.
References
Alliot, P. J., Delange, J. F., & Lekeux, A. (2015). VINCI, the European Reference for Ariane 6
Upper Stage Cryogenic Propulsive System. In 51st AIAA/SAE/ASEE Joint Propulsion
Conference (p. 4063).
ArianeGroup. (2021, February). Ariane 6 User Manual. https://www.arianespace.com/wp-
content/uploads/2021/03/Mua-6_Issue-2_Revision-0_March-2021.pdf
Boury, D., Cloutet, P., Cesco, N., Robert, E., Benedict, F., Plotard, P. (2013). Solid Rocket
Motors Technologies for Ariane 6. https://doi.org/10.2514/6.2013-4173
Burow, R., Just, D., Adamczyk, A., Jagels, C., Milke, A., Wendt, C., & Kneistler, H.
(2019, July). Thermal Control of the Cryogenic Upper Stage of Ariane 6. 49th
International Conference on Environmental Systems.
Dek, C., Overkamp, J., Toeter, A., Hoppenbrouwer, T., Slimmens, J., van Zijl, J., Areso Rossi,
P., Machado, R., Hereijgers, S., Kilic, V., & Naeije, M. (2020). A Recovery System for
the key Components of the First Stage of a Heavy Launch Vehicle. Aerospace Science
and Technology, 100, 105778. https://doi.org/10.1016/j.ast.2020.105778
Dias, N. (2018). Derivation of the French Space Operation Act Requirements in the
Specifications of the Future European Launcher Ariane 6. Journal of Space Safety
Engineering, 5(2), 121-125.
Erickson, L. K. (2010). Space flight: History, technology, and operations. Lanham, Md:
Government Institutes.
Gajeri, M., Aime, P., & Kezerashvili, R. (2021). A Titan Mission Using the Direct Fusion
Drive. Acta Astronautica., 180, 429–438. https://doi.org/10.1016/j.actaastro.2020.12.013
Hibbeler, R. C. (2007). Engineering Mechanics: Dynamics. Hoboken, N.J: Pearson Prentice
Hall.
Lee, J. R., & Dhital, D. (2013). Review of flaws and damages in space launch vehicle:
Structures. Journal of intelligent material systems and structures, 24(1), 4-20.
Maes, V. K., Pavlov, L., & Simonian, S. M. (. (2019). An Efficient Semi-Automated
Optimization approach for (grid-stiffened) composite structures: Application to Ariane 6
Interstage. Composite Structures, 209, 1042-1049
https://doi.org/10.1016/j.compstruct.2016.02.082
Malbéqui, P., Davy, R., & Bresson, C. (2015). Experimental Characterization of the Acoustics of
the Future Ariane 6 Launch Pad. In 7th European Conference for Aeronautics and Space
Sciences (pp. 23-38).
Merino, J., Patzelt, A., Steinacher, A., Windisch, M., Heinrich, G., Forster, R., & Bauer, C.
(2017). Ariane 6-Tanks and Structures for the New European Launcher. Deutsche
Gesellschaft für Luft-und Raumfahrt-Lilienthal-Oberth eV.
Mourey, P., Lambare, H., & Valbuena, M. F. (2014, June). Design of Launcher Towards
Spacecraft Comfort: Ariane 6 Objectives. In 13th European Conference on Spacecraft
Structures, Materials & Environmental Testing (Vol. 727, p. 75).
NASA. (2020). Gravity. https://www.nasa.gov/audience/forstudents/k-4/dictionary/Gravity.html
NASA. (2021, March 1). Space Launch Systems.
https://www.nasa.gov/exploration/systems/sls/factsheets.html
Patureau de Mirand, A., Bahu, J., & Gogdet, O. (2020). Ariane Next, a Vision for the Next
Generation of Ariane Launchers. Acta Astronautica, 170, 735-749.
https://doi.org/10.1016/j.actaastro.2020.02.003
Pelton, J. N., & Madry, S. (2020). Handbook of Small Satellites: Technology, Design,
Manufacture, Applications, Economics and Regulation. Springer.
Polonowski, R., & Clavier, R. (2019, June). Ariane Launchers Digital Engineering: Stakes and
Challenges. In 2019 8th Mediterranean Conference on Embedded Computing
(MECO) (pp. 1-5). IEEE.
Reddy, V. S. (2018). The SpaceX effect. New Space, 6(2), 125-134.https://www-liebertpub-
com.ezproxy.libproxy.db.erau.edu/doi/10.1089/space.2017.0032#B34
Resta, P. D., Monreal, J. A., Pouffary, B., Lemercier, S., Decadi, A., & Arnoud, E. (2019).
Ariane 6 Launch System Operational Concept Main Drivers. In Space Operations:
Inspiring Humankind's Future. Springer, Cham.
Rich, S. (2018). Europe Complains: SpaceX Rocket Prices Are Too Cheap to Beat.
https://www.fool.com/investing/2018/06/02/europe-complains-spacex-rocket-prices-are-
too-chea.aspx
The Soyuz Company. ( 2001, April). Soyuz User Manual.
http://www.starsem.com/services/images/soyuz_users_manual_190401.pdf
Uhlig, T., Sellmaier, F., & Schmidhuber, M. (Eds.). (2015). Spacecraft Operations. Springer
Vienna.
Comments